摘 要:光伏电站建成并网以后,运维上升成为光伏电站的工作重心,运维工作直接关系到电站能否长期正常稳定运行,关系到光伏电站的运维成本、投资价值及最终收益。文章就目前电站建设的两种设计解决方案:组串式逆变器方案与集中式逆变器方案,在涉及运维工作的各个方面:安全性与可靠性、运维难度与故障定位、故障导致损失、故障修复难度、防沙尘与防盐雾等进行对比。
关键词:光伏电站;集中式方案;组串式方案;成本与价值
前言
光伏电站依然在如火如荼的建设,现今国内光伏累计装机容量已超过28 GW,2013、2014连续两年新增并网光伏发电容量超过10 GW。随着光伏电站大规模建设并陆续并网,为保证光伏电站长期平稳运行,达到规划设计的发电目标,早日收回建站成本并实现盈利,运维工作自然而然成为光伏电站的重中之重。
目前电站设计因所采用逆变器不同而分为两种方案:集中式逆变器方案与组串式逆变器方案。
集中式方案采用集中式逆变器,单台容量达到500 kW,甚至更高。1 MW子阵需2台逆变器,子阵内所有组串经直流汇流箱汇流后,再分别输入子阵内2台逆变器。方案简图见图1。

组串式方案采用组串式并网逆变器,单台容量只有几十kW。1 MW子阵需约30台逆变器,子阵内光伏组串直流输出直接接入逆变器。方案简图见图2。
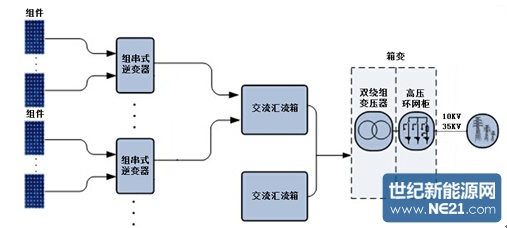
图2 组串式方案简图
因采用的方案不同,造成运维工作的难度及成本也有明显不同。下面从安全性、可靠性、故障率及故障定位精确性、巡检、故障影响范围及其造成的发电量损失、故障修复难度、防沙防尘等方面进行比较阐述。
1、安全性与可靠性比较
电站的安全运行及防火工作极其重要,而熔丝过热及直流拉弧是起火的重大风险来源。
1.1 集中式方案分析
组串输出需要通过直流汇流箱并联,再经过直流柜,100多串组串并联在一起,直流环节长,且每一汇流箱每一组串必须使用熔丝。按每串20块250 Wp组件串联计算,1 MW的光伏子阵使用直流熔丝数量达到200个,10 MW用量则达到2000个。如此庞大的直流熔丝用量导致熔丝过热烧坏绝缘保护外壳(层),甚至引发直流拉弧起火的风险倍增。
直流侧短路电流来自电池组件,短路电流分布范围广(几A~1.5 kA),在短路电流不够大(受光照、天气的影响)时,不能快速熔断熔丝,但短路电流可能大于熔断器的额定电流,导致绝缘部分过热、损坏,最终引起明火。例如,12 A的熔断器承载20 A电流,需要持续1000 S才能熔断,但熔断前绝缘部分就可能因过温受到损伤,电流继续冲击时就失去了绝缘保护,导致起弧燃烧。
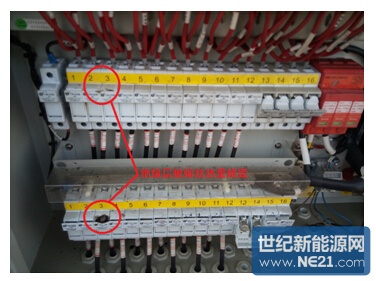
a. 发热熔丝烧毁绝缘外壳
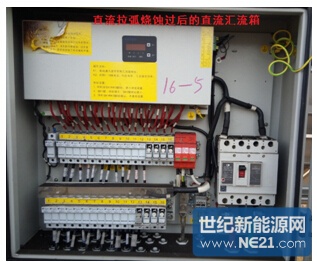
b. 直流汇流箱内拉弧灼烧痕迹
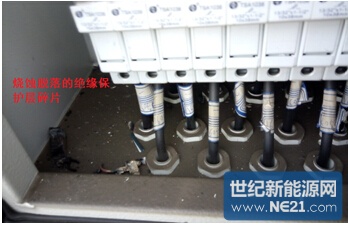
c. 烧蚀脱落的绝缘保护层碎片
图3 直流汇流箱内拉弧及烧蚀实景
1.2 组串式方案分析
组串式方案没有直流汇流箱,在直流侧,每一路组串都直接接入逆变器,无熔丝,直流线缆短且少,做到了主动安全设计与防护,有效抑制拉弧现象,避免起火事故发生;在交流侧,短路电流来自电网侧,短路电流较大(10 kA~20 kA),一旦发生异常,交流汇流箱内断路器会瞬时脱扣,将危害降至最低。
1.3 比较结果
组串式方案安全性更好,可靠性更高。
2、运维难易程度、故障定位精准度比较
2.1 集中式方案分析
对于集中式方案,多数电站的汇流箱与逆变器非同一厂家生产,通讯匹配困难。国内光伏电站目前普遍存在直流汇流箱故障率高、汇流箱通讯可靠性较低、数据信号不准确甚至错误导致无法通信的情况,因此难以准确得知每个组串的工作状态。即使通过其他方面发现异常,也难以快速准确定位并解决问题。
因此,为掌握光伏区每一组串工作状态,当前的检测方法是:找到区内每一个直流汇流箱,打开汇流箱,用手持电流钳表测量每个组串的工作电流来确认组串的状态。但在部分电站,由于直流汇流箱内直流线缆过于紧密,直流钳表无法卡入,导致无法测量。运维人员不得不断开直流汇流箱开关和对应组串熔丝,再逐串检测组串的电压和熔丝的状态。检查工作量大,现场运维繁琐且困难、缓慢,在给运维人员带来巨大工作量和技术要求的同时,也会危及运维人员的人身安全。

图4 直流汇流箱内密集的直流线缆
另外,检查期间开关被断开,影响了电站发电。假设单块组件最大功率为250 W,20块一串,一个16进1汇流箱装机容量即为16×5 kW=80 kW,完全检查一个汇流箱并记录共需10 min(0.17 h)。假设当时组串处于半载工作状态,断电检查一个汇流箱引起的发电量损失为80 kW×50%×0.17 h=6.8 kWh。
一个30 MW的电站拥有400多个汇流箱,全部巡检一次将花费大量时间,并损失数千kWh的发电量。再合并计算人工、车辆等成本投入,巡检所消耗的运维费用将十分可观。此种情况在山地电站表现会更加明显。需要特别注意的是,这样的巡检方式并不可靠,易产生人为疏忽,比如检查完成后忘记合闸,影响更多发电量。
目前不少电站的运维人员只有几个人,面对几十MW甚至上百MW的庞大电站,将难以全面检查到每个光伏子阵,更难以细致到每个组串,所以一些电站的汇流箱巡检约半年一次。这样的巡检频次,难以发现电站运行过程中存在的细小问题,虽然细微,但长期累积引起的发电量损失和危害却不可轻视。
目前国内光伏电站有关直流汇流箱运维的数据如下:
1)直流汇流箱内的熔丝:易损耗,维护工作量大,部分电站每月有总熔丝1%左右的维护量;且因工作量大,检修时容易出现工作疏漏,影响后续发电量。
2)直流汇流箱数据准确性与通讯可靠性:直流电流检测精度低,误差大于5%,弱光时难以分辨组件失效与否,不利于进行组件管理;直流汇流箱通讯故障率高、效果不佳,容易断链,导致数据无法上传,通讯失效后,组串监控和管理便处于完全失控状态,除非再次巡检发现并处理。
2.2 组串式方案分析
对于组串式方案,逆变器对每个组串的电压、电流及其他工作参数均有高精度的采样测量,测量精度达到5‰(见图5)。利用电站的通信系统,通过后台便可远程随时查看每个组串的工作状态和参数,实现远程巡检,智能运维。对于逆变器或组串异常,智能监控系统会主动进行告警上报,故障定位快速、精准,整个过程操作安全、无需断电、不影响发电量,将巡检、运维成本降至极低水平。
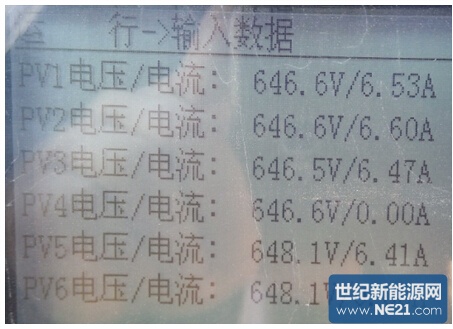
图5 组串式逆变器对组串电压、电流精确测量
2.3 比较结果
组串式故障定位快、精准,实现智能运维。
3、故障影响范围及其造成的发电量损失比较
电站建成运行一定时间后,各种因素导致的故障逐渐显现。
3.1 集中式方案分析
就采用集中式方案的光伏系统的各节点及设备而言,不考虑组件自身因素、施工接线因素及自然因素的破坏,直流汇流箱和逆变器故障是导致发电量损失的重要源头。
如前文所述,直流汇流箱故障在当前光伏电站所有故障中表现较为突出。一个1 MW的光伏子阵,一个组串(假设采用20块250 Wp组件,共5 kW)因熔丝故障不发电,即影响整个子阵发电量约0.5%;如果一个汇流箱(16进1出,合计功率80 kW)故障,即导致涉及该汇流箱的所有组串都不能正常发电,将影响整个子阵发电量约8%。因汇流箱通信可靠性低,运维人员难以在故障发生的第一时间发现故障、处理故障。多数故障往往在巡检时或累计影响较大时才被发现,但此时故障引起的发电量损失已按千、万计算。
如果一台逆变器遭遇故障而影响发电,将导致整个子阵约50%的发电量损失。集中式逆变器必须由专业人员检测维修,配件体积大、重量重,从故障发现到故障定位,再到故障解除,周期漫长。按日均发电4 h计算,一台500 kW的逆变器在故障期间(从故障到解除,按15 d计算)损失的发电量为500 kW×4 h/d×15 d =30000 kWh。按照上网电价1元/kWh计算,故障期间损失达到3万元。
3.2 组串式方案分析
同样不考虑组件自身因素、施工接线因素及自然因素的破坏,采用组串式方案的光伏系统因没有直流汇流箱,无熔丝,系统整体可靠性大幅提升,几乎只有在遭遇逆变器故障时才会导致发电量损失。组串式逆变器体积小,重量轻,通常电站都备有备品备件,可以在故障发生当天立即更换。单台逆变器故障时,最多影响6串组串(按照每串20块250 Wp组件串联计算,每个组串功率为5 kW),即使6串组串满发,按照日均发电4 h计算,因逆变器故障导致的发电量损失为5 kW×6×4 h/d×1 d = 120 kWh。按照上网电价1元/kWh计算,故障导致发电损失为120元。
考虑更极端的情况,电站无备品备件,需厂家直接发货更换,按照物流时间7 d计算,故障导致发电损失为120元/d×7 d= 840元。
3.3 比较结果
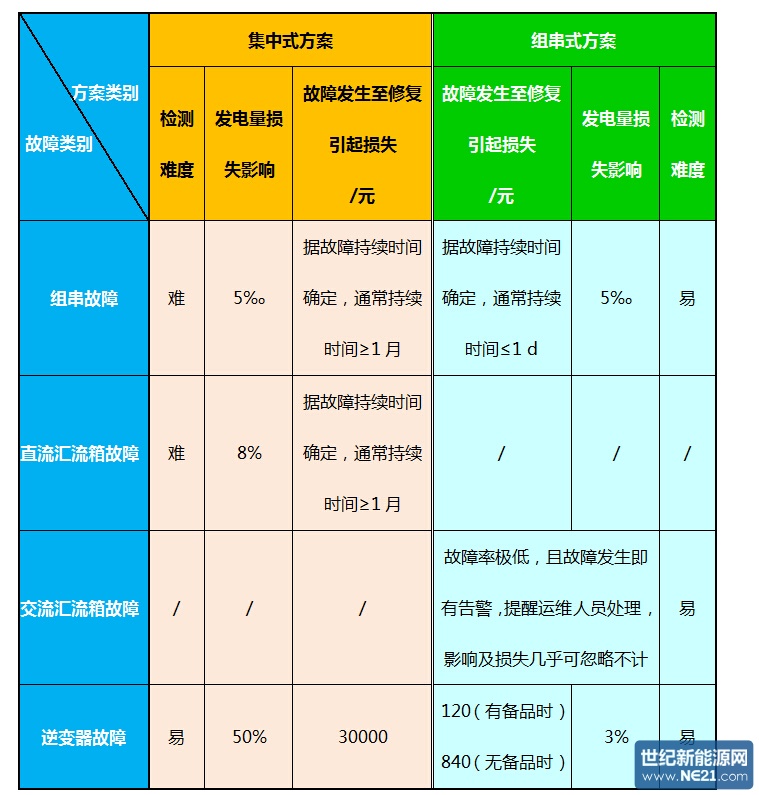
从表1可以看出,相比集中式方案故障损失动辄上万的情况,组串式方案优势显而易见,其因故障导致的损失仅相当于集中式方案的几百分之一到几十分之一。
4、故障修复难度比较
不同的方案特点不同,自然也导致了故障修复难度的差异。光伏电站所有组串全部投入后,故障修复工作主要集中在电站运行期间的线路故障及设备故障。线路故障受施工质量、人为破坏、自然力破坏等因素影响。设备故障包含汇流箱故障及逆变器故障。
4.1 集中式方案分析
直流汇流箱内原件轻小、数量少,线路简单,一旦故障准确定位后,修复难度不大;其修复困难集中表现为故障侦测或发现困难。
对于逆变器故障,因集中式逆变器体积大、重量重,内部许多元器件也同样具有此类特点,部分元件重量甚至达到数十或上百kg,给维护修复工作造成了较大程度的不便和麻烦。这也是电站建设时集中式逆变器采用整体吊装的部分原因所在。
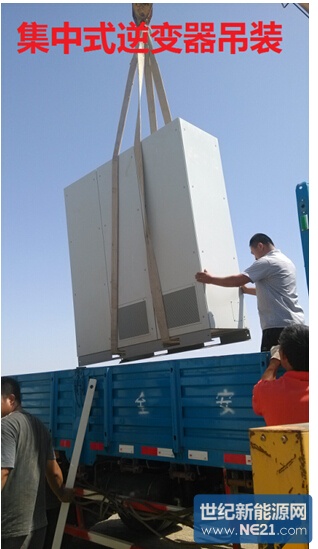
图6 集中式逆变器吊装
对于集中式逆变器方案,电站通常不会留存任何的备品备件,且集中式逆变器的维修必须由生产厂家售后人员完成。因此在故障发生后,必须要首先等待厂家人员前往电站定位问题;待问题定位后,确定维修方案及需要更换的元器件,然后再由逆变器厂家发货至电站现场,维修人员选用一定搬运车辆或工具将新的元器件搬运至逆变器房(箱)进行更换。一旦集中式逆变器出现故障,粗略估算整个维修过程将长达15 d,甚至更久,维修难度大、耗时长、费力多,还严重影响电站发电量。
4.2 组串式方案分析
组串式方案无直流汇流箱,所用交流汇流箱出现故障的概率几乎为零,甚至部分电站弃用汇流箱,将逆变器交流输出直接连接至箱变低压侧母线。因此,组串式方案的设备故障主要是逆变器的自身故障。相较于集中式逆变器的庞然大物,组串式逆变器显得异常轻灵小巧,其拆装、接线只需2人协作即可完成,且不必专业人员操作。因此,确认逆变器故障发生后,可根据精准的告警信息提示,立即启用备品替换故障逆变器,使电站短时间内全部恢复正常,将发电量损失降至最低。
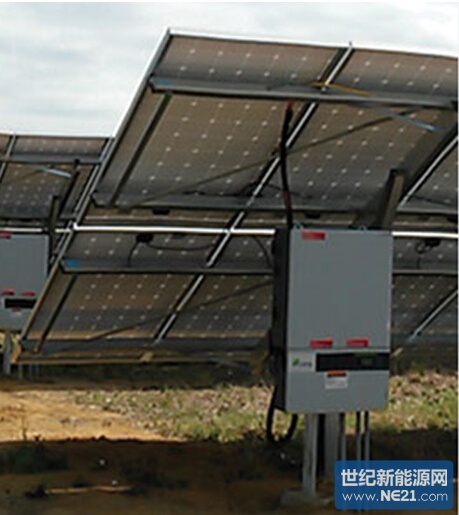
图7 组串式逆变安装
4.3 比较结果
综上所述,比较两种方案的故障修复难度,组串式方案故障修复难度小、速度快,优势明显。
5、防沙防尘、防盐雾比较
在逆变器使用寿命期限内,空气中的灰尘及沿海地区的盐雾对逆变器整体及内部零部件的寿命影响巨大。积累过多的灰尘可引起电路板电路失效或导致内部接触器接触不良,盐雾造成设备及元器件腐蚀,因此有逆变器在使用一段时间后,出现了控制失效、内部异常短路等现象,甚至起火燃烧,造成重大事故和损失。现阶段,灰尘和盐雾不可能被机房或设备防尘滤网完全过滤,因此,在风沙、雾霾严重的地区或沿海盐雾地区(也是我国土地资源和太阳能资源相对丰富的地区),两者对逆变器乃至光伏电站的长期安全正常运行构成了严重威胁。
5.1 直通风式散热方案
行业内集中式逆变器和逆变器房(箱),甚至部分组串式逆变器都普遍采用直通风式散热方案。空气中的沙尘、微粒等伴随逆变器和逆变器房(箱)中的空气和热量流动进入逆变器内部和逆变器房(箱),加之逆变器内部电子元器件的静电吸附作用,运行一段时间后,逆变器内部和逆变器房(箱)都沉积了大量的灰尘。同理,盐雾也会以同样的方式进入箱房及逆变器内部。
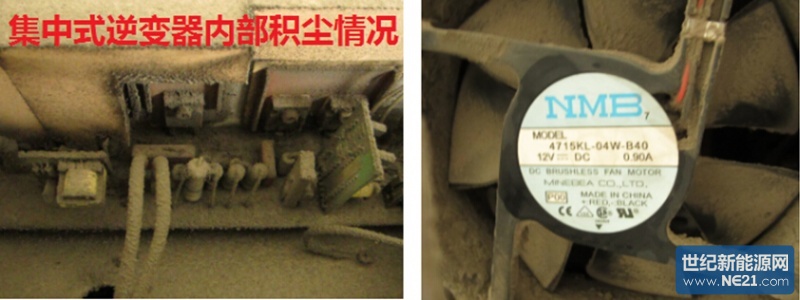
图8 集中式逆变器内部的积尘
5.1.1 灰尘及盐雾对电气设备的主要危害
1)漏电失效、腐蚀失效。在空气湿度较大时,吸湿后的灰尘导电活性激增,在元器件间形成漏电效应,造成信号异常或高压拉弧打火,甚至短路。同时,因湿度增加,湿尘中的酸根和金属离子活性增强,呈现一定酸性或碱性,对PCB的铜、焊锡、器件端点形成腐蚀效应,引起设备工作异常。在沿海高盐雾地区,腐蚀失效表现更加显著。
2)散热性能下降。积尘导致防尘网堵塞、设备散热性能变差,大功耗器件温度急剧上升,严重时甚至导致IGBT器件损坏。
5.1.2 运维清扫的困难及成本
多数光伏电站建设区域远离城市与乡村,给野外运维清扫工作造成诸多不便。另外,光伏电站白天要发电,清扫拆卸只能晚上进行。夏天逆变器房(箱)内温度高、蚊子多,冬天则是低温严寒,工作人员手脚活动都受到影响;设备的局部地方还需要用专业工具,如空气泵吹净灰尘。因此,清扫工作耗费了大量时间、人力和成本。
以西北风沙地区100 MW电站为例,10人1天只能清扫10台机器。100 MW共有200台机器,根据西北电站实际情况,每个月至少清扫一次,100 MW电站清扫一遍,正好需要20个工作日(1个月)。按此清扫频率,1人1天工资200元,10人1天需要2000元;按照1个月20工作日计算,1年人力费用就至少达到2000×20×12=48万;在电站的生命周期25年内,共需要25×48=1200万元。一个100 MW电站生命周期内的人力清扫费用就达到0.12元/W,这个成本相当惊人。如果进一步考虑25年内人力成本的上升和通胀因素,实际所付出的费用还要远高于这个数值。
另外,防尘网每隔1~2个月需要进行更换,还有专业的清洗工具采购和折旧、车辆及燃油投入,均给电站运维带来了实际的成本和困难。
5.2 热传导式散热方案
对于采用热传导式散热方案的逆变器,如国内厂家华为组串式逆变器,因逆变器采用非直通风式散热方案,逆变器的防护能力达到IP65,能够有效应对沙尘影响,即使在风沙及雾霾严重的地区,逆变器仍能轻松应对沙尘威胁,完全实现免清扫、免维护,节省大量清扫成本和投入。另一方面,华为组串式逆变器优异的热设计方案匹配性能优异的散热材料也保证了逆变器可以从容应对高温环境。IP65的防护等级和卓越的散热能力保证了组串式逆变器自身和光伏电站的长期、安全、正常、低成本运行。
5.3 两种散热方案比较分析
两种散热方案对比计算数据见表2。经比较,IP65防护等级具有明显优势。
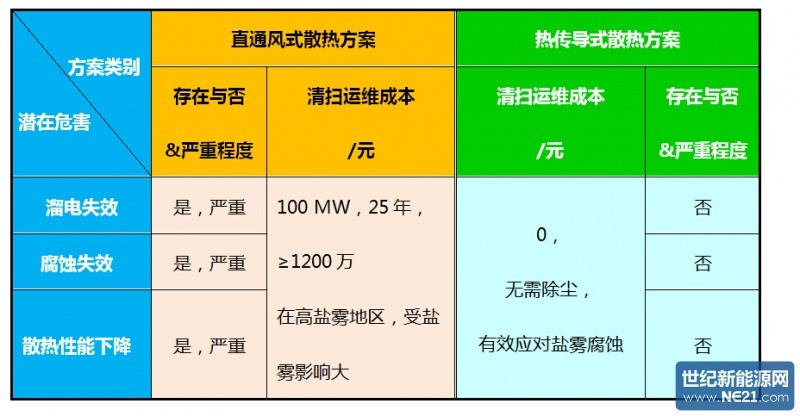
6、结论
从光伏电站运维所涉及的各工作层面对安全性和可靠性、运维难易程度及故障定位精确性、故障影响范围及其造成的发电量损失、故障修复难度、防沙防尘防盐雾等方面进行横向比较,结果显示:组串式逆变器方案更安全、更可靠;且可实现基于组串为基本管理单元的智能运维,极大地提升了运维工作效率、降低运维成本;同时显著降低了故障修复难度,大幅减少了故障导致的各种损失;IP65的防护等级使得逆变器可长期、正常、稳定运行在多沙尘、高盐雾的环境和地区,具有集中式方案难以比拟的优势。电站规模越大,地形越复杂(如山地电站),组串式方案的运维和成本优势越加显著,越能够为投资者降低电站运行成本,创造更多价值。
免责声明:本平台仅供信息发布交流之途,请谨慎判断信息真伪。如遇虚假诈骗信息,请立即举报
举报