1、技术背景
我国钢铁行业大力发展和推广余热发电技术是促进钢铁产业技术升级和结构调整、提高环境保护和资源综合利用水平的有效途径,也是钢铁企业提高产品质量和降低生产成本,增强产品市场竞争力的重要途径。
目前钢铁企业连续性可利用余热及易于回收的余热大都已实施了回收利用措施,而炼钢环节中存在的大量温度、流量、压力等参数波动较大的间歇性余热难以得到高效利用,即使采用了储热装置来满足连续发电的要求,但由于热源不稳定,难以形成高温高压的高品质蒸汽,只能采用低参数饱和蒸汽轮机发电,导致发电效率低下,而且运行方式只能以余热定蒸汽量,不能灵活调节电力输出,无法满足电力调峰需求。
2、技术方案
钢铁企业的转炉炼钢工艺是产生间歇性余热的主要环节,在一个冶炼周期内,分为装料、吹炼和出钢三个步骤,把装入的铁水经过吹氧,完成降碳、升温、脱磷等高温物理化学反应,最后排出大量的CO、CO2等高温废气,这种工艺决定了转炉高温烟气具有间歇性,波动性和周期性[1,2],如下图1所示
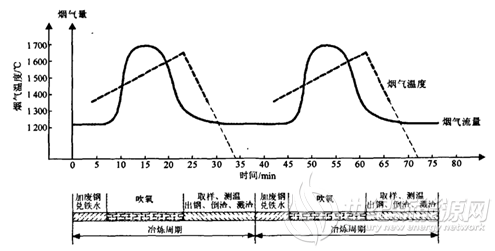
图1 转炉烟气流量及温度曲线
转炉炼钢排出的大量CO、CO2废气温度高达1400-1600℃,能耗约占整个钢铁生产中能耗的8%~14%,仅次于炼铁工序,其中45%的能耗以废气的散热形式直接排放到大气中,不仅造成环境的污染,而且浪费了大量的优质高温热能资源[3]。
2.1 基于蒸汽储热器的余热发电方案
某钢铁厂有3台80t/h转炉,采用烟道蒸汽余热锅炉,产生蒸汽32t/h。由于转炉烟气和余热锅炉蒸汽的间歇性和波动性特点,方案采用蒸汽储热器实现蒸汽输出的连续性和稳定性,系统工艺图如下图2所示[4,5,6]。

图2 基于蒸汽储热的转炉余热发电系统工艺图
如上图所示,基于蒸汽储热器的转炉余热发电系统主要包括汽化冷却烟道余热锅炉、饱和蒸汽轮机、发电机三大主体设备及蒸汽储热、排气冷却(空冷系统或水冷系统)、给水除氧三大汽水系统。
汽化烟道余热锅炉采用水/中低压蒸汽作为换热介质,蒸汽压力为0.8-1.3Mpa,转炉炼钢期间产生的平均蒸汽流量为10.6t/h,3台合计32t/h。
蒸汽储热器入口蒸汽压力为1.0~1.3MPa,出口蒸汽压力为0.4~0.6 MPa,有效储热体积为200m3。
转炉余热发电系统通常配置中小容量饱和汽轮机组,各有关设计变量的选取参考设计手册及现场运行经验获取[4],进汽压力为0.5MPa,排汽压力为8kPa。根据饱和蒸汽轮机进汽参数,查表得到进汽焓h0为2748.5kJ/kg;根据排汽压力并计算蒸汽等熵焓降的理论排汽焓为2124.3kJ/kg,根据参考文献[7],取汽轮机内效率为0.75,可计算得到汽轮机实际排汽焓hc为2280.4kJ/kg,按照如下公式,计算汽轮机发电功率为3643kW。
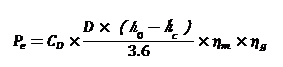
上式中,Pe为汽轮机发电功率,单位是kW,CD为蒸汽流量修正系数0.96,D为蒸汽流量,ηm为汽轮机机械效率0.95,ηg为发电机效率0.96。
2.2基于熔盐储热的余热发电方案
为充分利用转炉烟气的高温余热,进一步提高优质高温热能的利用效率,基于熔盐储热的转炉余热发电方案需要将现有的汽化烟道余热锅炉改造为熔盐余热锅炉,将换热介质由饱和蒸汽改为熔融态熔盐,系统示意图如下图3所示。
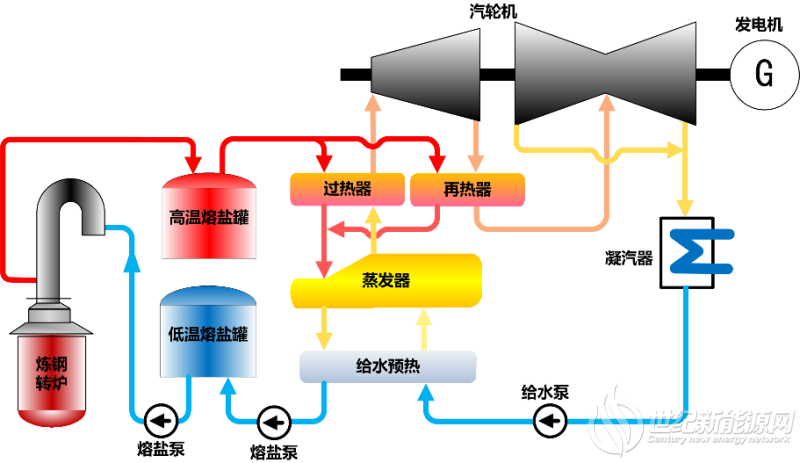
图3 基于熔盐储热的转炉余热发电系统工艺图
烟道熔盐余热锅炉将温度和流量大幅波动的高温烟气热量转化为熔融态熔盐的显热,吸热后温度升高的高温熔盐送入高温熔盐罐;当系统需要发电时,将高温熔盐依次泵入熔盐/蒸汽过热器、熔盐/水蒸发器和熔盐/水的给水预热器,逐级加热给水,产生高温高压蒸汽,换热后的熔盐温度降低,送入低温熔盐罐,完成储能循环;如需进一步提高发电效率,还可增加再热器,如图3所示。
熔盐选用太阳能光热发电中应用广泛的二元熔盐solar salt[8],由60%的硝酸钠和40%的硝酸钾组成,熔点为220℃,在600℃以下有良好的热稳定性。这种储热介质有如下特性[9]:①使用温度范围290℃~550℃,热稳定性好;②低的蒸汽压,熔盐具有较低的蒸汽压,特别是混合熔盐,蒸汽压更低;③热容量大;④较低的粘度;⑤具有化学稳定性。由于熔盐的蒸汽压力较低,余热锅炉换热材料不必选用高压厚壁材料,因此能够降低余热锅炉的设计难度和制造成本。
根据转炉炼钢高温烟气的生产特点,熔盐储热系统需要满足间歇吸热、持续放热的要求;按照3台80t/h转炉的放热量计算,熔盐的总储热量为6MWh,熔盐工作温度区间290℃~550℃,熔盐总量80t,熔盐储罐尺寸为Φ4m×3.2m,主设备技术参数如下表1所示。
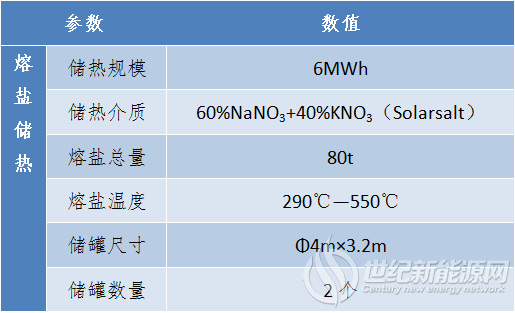
表1熔盐储热技术参数表
以稳定的高温熔盐为热源,可以方便的生产高温高压蒸汽,大幅增加余热发电功率和效率。这里选用汽轮机进汽参数为高压参数8.8MPa,535℃,进汽焓h0为3477 kJ/kg,取汽轮机内效率为0.8,汽轮机实际排汽焓hc为2317 kJ/kg,计算得到汽轮机发电功率为7396kW,技术参数如下表2所示。
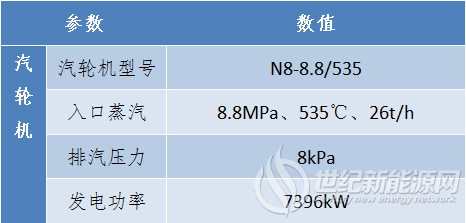
表2基于熔盐储热方案的汽轮机技术参数表
3、经济性分析
3.1 主要技术参数对比
为充分利用转炉炼钢1400-1600℃间歇性高温烟气热量,分别采用蒸汽储热器和熔盐储热技术方案进行余热发电系统设计,两种技术方案的主设备方案有所不同,其中蒸汽储热器方案主设备主要有汽化余热锅炉,蒸汽储热器和汽轮发电机组;熔盐储热方案主设备包括熔盐余热锅炉,熔盐储热设备,熔盐/水换热设备和汽轮发电机组,如下表3所示。
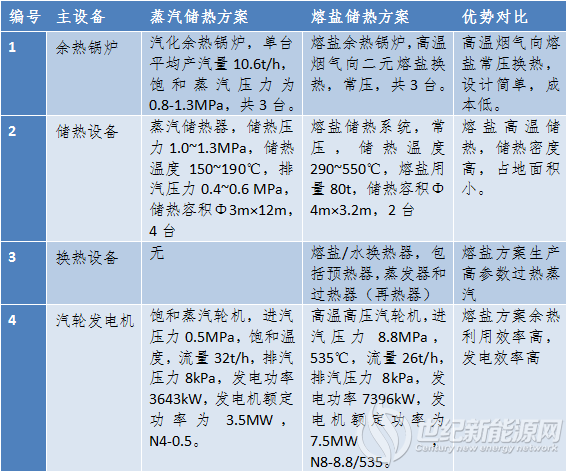
表3主设备技术参数对比表
从上表可以看出,在采用相同的余热资源条件下,熔盐储热方案能够充分利用高温余热的高品位热能,提高能量利用效率,发电量能够达到蒸汽储热方案的2倍,具有较大的技术优势和高效能源利用优势。
3.2 经济性比较
(1)蒸汽储热器方案
蒸汽储热器方案的投资概算参考文献[10]的相关数据,项目概算包括两部分,主体部分包括土建、热力、电气、消防、仪表、烟道改造、给排水;厂房外围部分包括热力管道、给排水、暖通、电气、总图、仪表等,工程总投资为3988.41万元,单位KW投资为9971万元/KW。
发电收入方面,余热发电运行小时按7500小时测算,电价为0.5元/kWh,厂用电率为7%,项目年发电收入为1271万元,投资回收期为3.1年。
(2)熔盐储热方案
转炉炼钢高温余热采用熔盐作为换热储热介质,既可以保持高温余热的高品质热能,也能够避免压力换热储热设备的使用,有效降低换热和储热成本,并提高储能密度,可以大幅提高高温余热的利用效率和项目经济性,项目概算工程总投资为5279.7万元,单位千瓦投资为6599元/KW。
熔盐储热方案的发电收入方面,按照发电时间7500小时,电价为0.5元/kWh,厂用电率为8%,项目年发电收入为2551.7万元,投资回收期为2.1年。
2.3对比分析
从工程概算投资和发电量对比可知,采用熔盐储热方案的发电量比蒸汽储热方案提高1倍,而投资仅增加32.3%,使投资回收期从3.1年减少到2.1年,显著增加项目的经济性。
4、结论
我国钢铁工业的快速发展,面临着越来越严峻的资源、能源瓶颈制约,开展余热余能的回收利用是降低钢铁生产能源消耗的有效方式,目前转炉炼钢的间歇性高温余热回收利用主要是通过转炉烟道汽化余热锅炉回收热能,采用蒸汽储热器存储热能,利用低品质饱和蒸汽发电实现余热的回收和利用,高温热能利用率不高,存在较大的能源浪费。
采用熔盐余热锅炉回收高温余热,可以保持高温余热的高品质热能优势,降低高温烟道换热器设计难度和成本,采用高参数蒸汽发电,可以大幅提高发电量,有利于降低企业的发电成本,有利于钢铁企业降本增效,具有很好的市场推广价值。
另外,采用熔盐储热发电方案,可以快速调节蒸汽输出、调节发电机输出功率,具有很强的发电灵活性,适合跟踪用电负荷波动,也可用于电网调峰。
参考文献
[1]朱苗勇.现代冶金学[M].北京:冶金工业出版社,2005,190-193.
[2]冯聚和.炼钢设计原理[M]北京:化学工业出版社,2005:119-123.
[3]张芳.转炉炼钢[M].北京:化学工业出版社,2008
[4]赵斌.转炉饱和汽轮机选型计算与分析[J].汽轮机技术,2010,52(1):l7-20
[5]王毅等. 钢铁厂饱和蒸汽发电系统及设备研究[J].钢铁技术,2007,(2):56-58
[6]潘秀兰等.转炉烟气回收和利用技术的最新进展[J]冶金能源,2010,(5):37-42
[7]小型热电站实用设计手册编写组,小型热电站实用设计手册【M】,北京:中国电力出版社,1989.
[8] Craig E.TYNER, J. Paul Sutherland, William R. Gould. SOLAR TWO: A Molten Solar Power Tower Demonstration, Sandia National Laboratories, SAND95-1828C
[9] 谢刚. 熔盐理论与应用【M】. 北京:冶金工业出版社, 1998. 1-9
[10] 李洪福. 炼钢转炉烟气余热回收利用研究[D]. 山东大学, 2006.
免责声明:本平台仅供信息发布交流之途,请谨慎判断信息真伪。如遇虚假诈骗信息,请立即举报
举报